In a rapidly-changing global marketplace, remaining flexible and adaptable in business is vital. But how do you stay nimble and grow your business at the same time? Learning how to harness the power of lean manufacturing principles might be the key.
No longer just for large companies, lean manufacturing concepts can be applied to businesses of any size.
Applying these principles can not only improve productivity, efficiency and profitability, but transform the way you run your business and give you that all-important competitive edge.
Sound complicated? It’s not. Here, we’ll explore what lean manufacturing principles are and how you can apply them to your own business.
How to use lean principles in your business
Whether you sell handmade soap or run a graphic design business, you can use these principles to produce more with less waste.
- Talk to your customers.
- Standardise your processes.
- Reduce excess inventory.
- Shorten production cycles.
- Speed up response times.
- Quality-test your products or services.
- Empower your staff.
- Partner with your suppliers.
Not exactly sure what lean manufacturing means? Let me explain.
What is lean manufacturing?
Lean manufacturing is essentially about providing better value for your customers while using fewer resources.
Lean is about doing more with less.
Lean is both a philosophy and a system that eliminates waste and promotes continuous improvement and flow throughout your business — all while delivering the best possible product to your customers as quickly as possible.
Pioneered by Toyota in Japan for their motor vehicle assembly process, the lean methodology has gained momentum worldwide and is now used in a broad range of industries.
Getting rid of waste
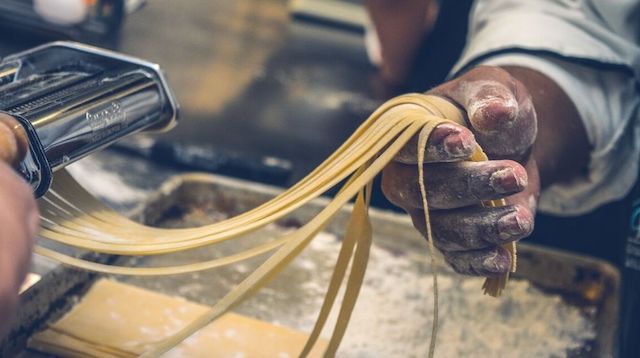
Reducing or eliminating waste, or that which does not add value, is a key part of lean manufacturing. Waste can take different forms, depending on the type of business you have. Examples of waste include:
- Defects and overproduction
- Overly complex processes
- Waiting time
- Excess inventory
- Wasted skills and talents
Lean manufacturing focuses on reducing waste in order to deliver positive benefits to your business.
Steps to a lean manufacturing approach
When business owners first start out, they’re often using lean principles by virtue of having fewer resources at their disposal. So they instinctively tend to be shrewd about how and when they use those resources for maximum benefit and minimal waste.
Once cash flow improves, many small businesses outgrow their lean beginnings without even realising it.
But there are ways to maintain these principles and continue to reap the rewards.
1. Talk to your customers
The first place to start is by focusing on your customers. Who are they and what do they need right now that you can provide?
Get things right quickly by seeking input from your customers.
Many businesses get caught up in developing products and services without first identifying their customers’ core needs. They end up with a product that doesn’t meet actual customer needs, which is ultimately a waste of time and money.
2. Standardise your processes
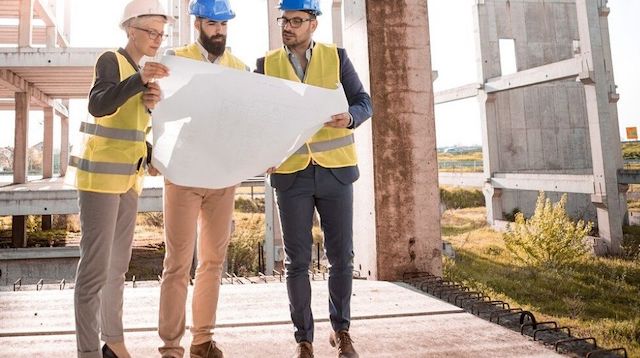
Small businesses often tend to grow ad hoc, which usually becomes unworkable at a certain point.
Standardising your processes is a key part of going lean. Identify wasteful activities and find more efficient ways of doing things that add value to your bottom line. How long does it take to do or make a thing? How can that process be improved? Are there any unnecessary steps that can be joined with others or even eliminated altogether?
3. Reduce excess inventory
Traditional production is driven by a sales forecast, often resulting in excess inventory. Maintaining excess inventory though, can tie up resources, slow down response time and complicate quality-control issues, especially if the stock becomes obsolete before it can be sold.
By contrast, lean production is led by customer demand.
This means producing smaller batches, which cuts down on inventory. By producing stock when requested by the customer, you can:
- Make more use of your warehouse space
- Double your output from the same size space
- Make better use of your employees’ time
Operational planning can be useful here.
4. Shorten production cycles
The length of your production cycle determines how quickly you convert assets into profits. What used to take days or weeks can now often be done in a matter of hours, so make use of the technology at your disposal.
5. Speed up response times
It’s important to be adaptable to any changes in the market and to respond accordingly.
But speeding up your response times isn’t about just working faster, which is ultimately unsustainable and can lead to error. It’s about improving the overall workflow and streamlining your processes, so you can respond more quickly to market demands and make the most of opportunities.
6. Quality-test your products or services
When your customers receive consistently high-quality products and services, they will quickly become loyal, raving fans. So it’s important to employ quality-control methods in your business.
Create testing procedures and controls at several checkpoints in the process to detect any problems early on. Make corrections quickly and move forward. You will end up with better goods and services, and happier customers to boot.
7. Empower your staff
The success of lean manufacturing relies on having an involved and supportive workforce. Give your employees the power to make decisions about their jobs and tasks, and provide them with the right tools to do so.
Make it everyone’s job to measure work progress and improve techniques so they can start to look for blockages themselves. Empowering your staff in this way will boost morale and performance, a key factor in increasing productivity and efficiency.
8. Partner with your suppliers
Traditionally, buyers and suppliers are seen as opposing forces, or at least competitors. Each tries to get the best possible price that benefits their business.
With a lean approach, the focus is on cooperation.
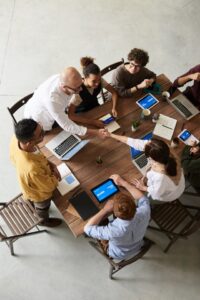
Where appropriate, reach out to your suppliers to become ‘partners’ in the lean manufacturing process. The benefits of eliminating waste and increasing value can go both ways, and as an added bonus, helps strengthen relationships.
The lean benefits
The small business benefits of going lean are substantial. By reducing waste, your business can:
- Save time and money, which can be passed on to customers in lower prices
- Improve service and quality
- Increase team productivity and morale
Small businesses tend to survive day to day and often don’t take time out to assess their direction. No matter the size of your business, you can’t afford not to plan. Lean manufacturing principles can help keep your business moving in the right direction.
Are you ready to get lean?
Lean manufacturing is more than just a way to make products. It’s a way of thinking, a mindset. Through simple innovations, you can make your business more resourceful and competitive but also adaptable to changes in the marketplace.
Applying these principles is not an end point. It’s something that constantly evolves and is continuously improving your business. By eliminating waste and improving productivity, efficiency and profitability, you can turn your business into a lean and nimble success story.