Your supply chain is the sequence of processes that move your product from production through distribution, all the way to delivery. And depending on how well things run, your supply chain management (SCM) is either a competitive advantage for your business or a disadvantage.
Either you are getting materials from the manufacturer to the customer in as few steps as humanly possible, or you are hemorrhaging money at every step. There seems to be absolutely nothing in between these days.
We have been shipping goods for as long as there have been trucks on the road.
However, it hasn’t been until recent years that technology and strategic thinking really changed how businesses looked at their supply chain. They started to see all of the waste and all of the opportunity.
Reduce waste, save money with these 4 tips
If your small business sells goods or services, you rely on others to do what you do. Here’s how to fine-tune your supply chain process for cost savings and improved productivity.
- Embrace technology.
- Decide whether to outsource or hire in-house.
- Anticipate demands and trends.
- Seek and destroy waste or repetition.
Could you be doing things better? Is the way you’re managing your supply chain (or not) currently hurting your bottom line? Ask yourself if any of these tips would help.
1. Embrace technology
If you’re currently running your supply chain yourself, today’s SCM tools can help you see the bigger picture and keep operations under control.
On the other hand, if you have a full-time employee to manage your supply chain for you, they will need tools to track the day-to-day data to find indicators of waste.
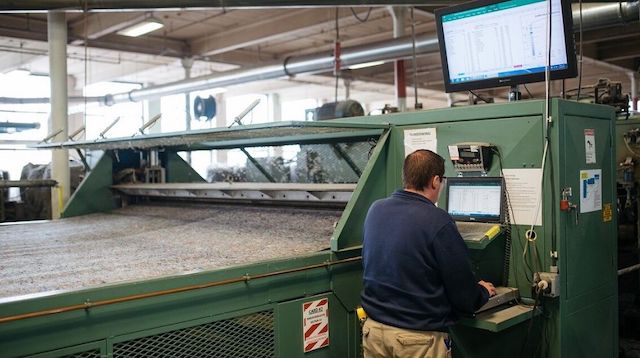
Some of the most popular SCM tools for small to medium-sized businesses (SMB) include:
- Oracle’s Netsuite
- IBM’s Supply Chain Management
- TradeGecko
- ASC Supply Chain Software
- OurRecords Compliance Network
Each platform has its own pros and cons so it’s best to demo as many as possible before making a decision.
2. Anticipate demands and trends
If you can anticipate a spike in demand for a certain product or offering, you won’t be scrambling to meet orders when the time arrives.
Pretty much every industry has seasonal shifts and trends they need to prepare for.
A simple example would be a department store knowing to stock up on Halloween costumes well before October. A few other examples might be:
- A hardware store anticipating they are going to need more lawn goods for the spring
- A pharmacy knowing to stock up on cold medication for flu season
You are probably already aware of a number of seasonal trends within your own industry. Account for those, but take a good long look at a calendar and see if there is anything else you can prepare for.
3. Decide whether to outsource or hire in-house
Once your operations reach a certain level, you may think about hiring an SCM company to take over that side of the business.
Or would it be more cost-effective to hire an in-house supply chain manager?
Either of these choices can really benefit any company. The more goods or services you deliver, the more a “little hole” in your supply chain process can drain your profits.
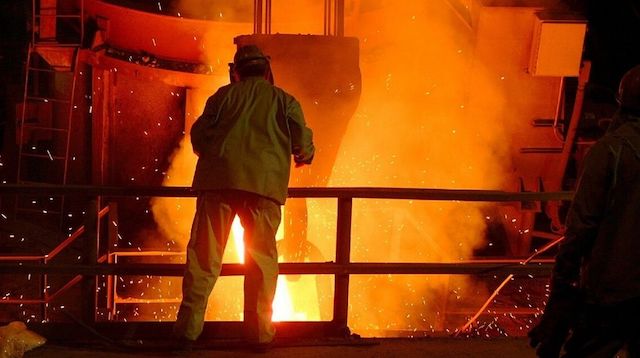
To hire a full-time employee will cost you about 1.4 times their salary when you factor in things like:
- Bonuses
- Vacation time
- Parental leave
- Benefits packages
It can also cost an additional $4,000 and take up to 52 days just to find a qualified applicant. And you need a qualified applicant. You probably don’t want to give somebody their first job in this field. Their mistakes on the job will have a very big impact on your bottom line. There’s a lot at stake.
The outsourcing option
On the other hand, outsourcing to an SCM company might make more sense, depending on where you are in your business growth.
The cost of hiring an SCM firm could either be more or less than hiring a full-time employee.
There are a lot of variables such as the:
- Size of your organization
- Size of your team
- Industry you’re in
- Location of all your facilities
- Type of goods or services you produce
Whether or not you hire a full-time employee, this is a full-time task. The bottom line is you will reach a certain point where you don’t have time to worry about it, and you need to hand this off to someone you can trust.
4. Seek and destroy waste or repetition
This should be the first item of business for the company or person you bring on to handle your SCM.
You’re probably not doing business on the same scale as Starbucks, but you can still learn from their expensive mistakes.
Case study: Starbucks
It’s hard to imagine, but there was a time when the mega-company’s SCM was killing their profitability.
Right around the downturn of the economy in 2006, their supply costs were at an all-time high and rose by over $75 million in one year alone.
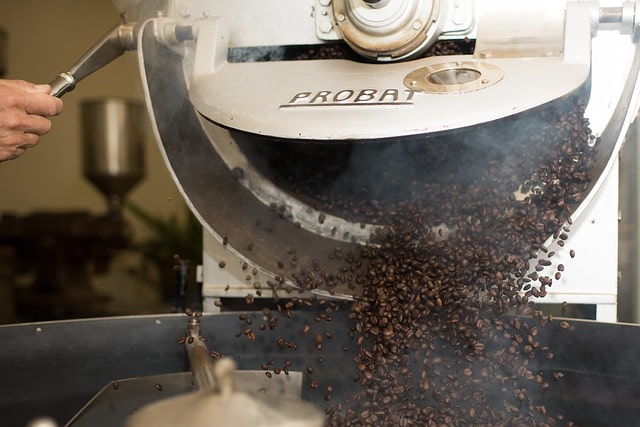
They put a new team in place to slash costs and simplify their fragmented supply chain. They ended up doing the following:
- Reducing the number of companies/vendors they outsourced to
- Defining roles more clearly, both internally and externally
- Opening a fifth roasting plant location
- Introducing scorecards so they had clear metrics for success
- Negotiating for better prices from vendors
- Eliminating all non-value adding activities
Starbucks’ efforts helped them slash their supply chain costs by half a billion dollars in two years.
If you’re a small or medium-size business, opening a new facility likely isn’t going to save you money. However, you can learn from all of the other steps they took to take a close look at your own relationships, staff and processes.
Fine-tune your supply chain process
The more your company grows, the more a leaky supply chain can stand in the way of profitability. Every new product you introduce, or territory you reach, holds the potential to throw your whole system for a loop and silently bleed your profits dry.
The sooner you start watching your supply chain, the easier it will be to scale these systems as you grow.
And the sooner your SCM stops being a liability, the sooner it becomes an advantage.
This post does not represent an endorsement of any of the products mentioned here. Information was accurate as of publication date.